Understanding Manufacturing Resource Planning
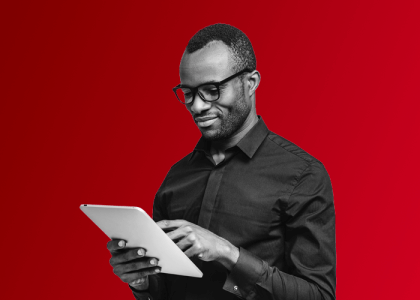
If you want to grow your manufacturing business, you need to have systems in place that can help you maximise your efficiency and reduce waste. What tools are out there to support you?
Manufacturing Resource Planning (MRP) is a system that manufacturers use to effectively plan how they use resources.
A manufacturing company lives and dies by its ability to maximise the efficiency of its production schedule. They need to minimise costs but to get the most out of each resource. That means delays have to be avoided, so you’ll need to plan ahead with sales forecasting. That way you won’t hold up your processes while you wait for stock to come in.
A MRP should be integrated into your other solutions so you can centralise your decision making.
You may see references to MRP II, which is a more common solution in the modern day. MRP II was developed in the 1980s. It integrates with account systems and enabled better inventory forecasting. Think of MRP II as an improvement on MRP I.
Benefits of Manufacturing Resource Planning
When you only need to make a few products, the manufacturing process can be pretty simple. But scaling up increases complexities, so you’ll start to need an MRP to keep up with your competitors. There are three core benefits that come from MRP.
Improvement in Production Efficiency
Simply put, if you always have the amount of materials you need to make products, you won't have any downtime. That means your production process never has to slow down, which keeps efficiency high.
Cost Reduction and Profitability
MRP will ensure that you're buying the exact amount of stock that you need to meet demand with a flex to support unforeseen circumstances. You won't have to waste money on needed stock that won't get sold, as you can use forecasting to predict sales trends. This maximises profitability.
Enhanced Customer Service
Reducing the risk of delays has an immediate impact on your customers, as you’re less likely to go out of stock. That means no one has to wait to receive your product, making everyone a lot happier.
How Does Manufacturing Resource Planning Work?
MRPs run through the entire business, tracking a lot of different activities and events across your systems.
Define what’s being produced, and exactly what goes into the production of each item. You’ll also want to spell out the quantities you need and by what date. Exactly how you do this depends on what kind of business you are. If you are a make-to-stock company, you’ll need forecasting to make a reasonable prediction. If you’re a make-to-stock business, you can rely on customer order numbers.
All this information gets put into a master production schedule (MPS). This is used to indicate what will be produced over a given period.
Technology gets used to speed this process up. Imagine having to keep track of all this manually? That’s relatively simple when you’re making a few products to order, but if you want to have a hope of scaling up, you’ll need to embrace technology. This will also ensure that you’re using more accurate data, which reduces further reduces the risk of errors and blockages.
Implementing Manufacturing Resource Planning in Your Business
Whenever you implement any kind of new system in your organisation, you’ll want to create a project team. This should include a project manager, application developers and analysts and stakeholders from across the business.
This team should take a look at your current setup and evaluate it. What issues are you facing? What works? Use this feedback to create a plan on what your new process will look like. This will help you create a timeline to keep the project on track.
Before the system is in place, make sure you have a very robust training plan. This will ensure you get good adoption rates, which an MRP particularly relies on.
As you approach your go-live date, you’ll need to make sure you test regularly, using any data you can. This will help you make sure everything’s working as intended.
Future Trends in Manufacturing Resource Planning
Manufacturing trends are always shifting in response to market pressures. New technology can also inform
One of the most key trends is the role of cloud-based systems that utilise the Internet of Things (IIoT). These systems enable data to be used more effectively from anywhere, which suits the often more mobile workforces that manufacturing businesses require.
AI is also a hot button topic, with new developments being factored into MRP all the time. For example, AI can be used to make better and quicker decisions. If an AI identifies that you’re running low on a certain material, it can make independent decisions to order that material.
One key implication of both these trends is that you’ll need to make sure you hire talent that has the skills to work with new technology or provide opportunities to upskill.
Want to learn more about what trends are going to impact the manufacturing industry? Get in touch us, or check out our manufacturing industry landing page.